Corrosie is de schade of verslechtering van materialen of hun eigenschappen veroorzaakt door de werking van de omgeving.De meeste corrosie vindt plaats in de atmosferische omgeving, die corrosieve componenten en corrosieve factoren bevat, zoals zuurstof, vochtigheid, temperatuurveranderingen en verontreinigingen.
Zoutsproeicorrosie is een veel voorkomende en meest destructieve vorm van atmosferische corrosie.Zoutsproeicorrosie op het oppervlak van metalen materialen wordt veroorzaakt doordat de chloride-ionen in het metaaloppervlak door de oxidatielaag en beschermende laag dringen en door de interne elektrochemische metaalreactie.Tegelijkertijd bevat het chloride-ion een bepaalde hoeveelheid hydratatie-energie, die gemakkelijk kan worden geadsorbeerd in de poriën en scheuren van het metaaloppervlak en om de zuurstof in de oxidelaag te vervangen, waardoor het onoplosbare oxide wordt omgezet in oplosbaar chloride en het gepassiveerde toestandsoppervlak omzetten in een actief oppervlak.
Zoutcorrosiebeschermingsspraytest is een omgevingstest waarbij voornamelijk gebruik wordt gemaakt van de kunstmatige gesimuleerde omgevingsomstandigheden van zoutsproeitestapparatuur die worden gecreëerd door zoutsproeitestapparatuur om de corrosieweerstand van producten of metalen materialen te beoordelen.Het is onderverdeeld in twee soorten tests: blootstellingstests in de natuurlijke omgeving en kunstmatig versnelde simulatie-omgevingstests met zoutsproeien.
In een kunstmatige simulatie van een zoutsproeiomgevingstest wordt de zoutsproeitestkamer met een bepaald ruimtevolume gebruikt en wordt de zoutsproeiomgeving gegenereerd door kunstmatige methoden in het ruimtevolume te gebruiken, om de prestaties en kwaliteit van zoutsproeicorrosie te beoordelen weerstand van producten.
De zoutconcentratie van chloride in de zoutsproeiomgeving kan meerdere malen of tientallen keren hoger zijn dan het zoutsproeigehalte in de gewone natuurlijke omgeving, waardoor de corrosiesnelheid aanzienlijk wordt verhoogd en de tijd voor het verkrijgen van de resultaten aanzienlijk wordt verkort.Het kan bijvoorbeeld een jaar duren voordat het product corrodeert bij het testen van een productmonster in de natuurlijke omgeving, terwijl je al na 24 uur vergelijkbare testresultaten kunt krijgen in de kunstmatige simulatie-zoutsproeiomgeving.
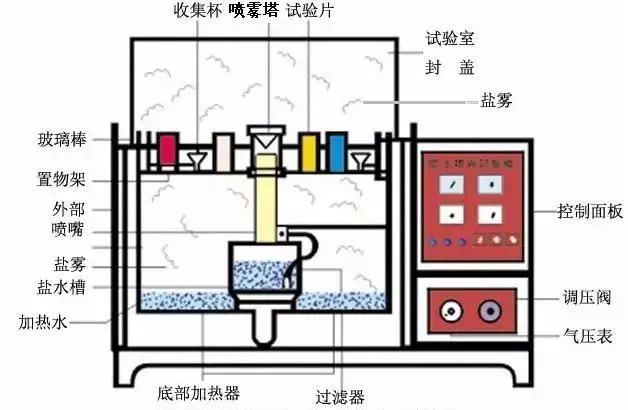
Laboratorium gesimuleerde zoutnevel kan worden onderverdeeld in vier categorieën.
(1) De neutrale zoutsproeitest (NSS-test) is de vroegste en meest gebruikte versnelde corrosietestmethode.Het maakt gebruik van een zoutwateroplossing van 5% natriumchloride, waarbij de pH-waarde als sproeioplossing is ingesteld op een neutraal bereik (6,5 ~ 7,2).De testtemperatuur is 35 ℃ en de vereiste sedimentatiesnelheid van zoutnevel is 1 ~ 2 ml/80 cm/uur.
(2) De azijnzuurzoutsproeitest (ASS-test) is ontwikkeld op basis van de neutrale zoutsproeitest.Het zit in een 5% natriumchlorideoplossing met wat ijsazijn, zodat de PH-waarde van de oplossing wordt verlaagd tot ongeveer 3, de oplossing zuur wordt en de gevormde zoutnevel uiteindelijk zuur wordt door neutrale zoutnevel.De corrosiesnelheid is ongeveer 3 keer sneller dan die van de NSS-test.
(3) De koperzout-versnelde acetaatsproeitest (CASS-test) is een nieuw ontwikkelde buitenlandse snelle zoutsproeicorrosietest.De testtemperatuur bedraagt 50 ℃.Aan de zoutoplossing wordt een kleine hoeveelheid koperzout-koperchloride toegevoegd om corrosie sterk te induceren.De corrosiesnelheid is ongeveer 8 maal die van de NSS-test.
(4) De afwisselende zoutsproeitest is een uitgebreide zoutsproeitest, die eigenlijk een neutrale zoutsproeitest is plus een test met constante vochtigheid en hitte.Het wordt voornamelijk gebruikt voor producten van het holtetype.Door het binnendringen van het getijdenmilieu ontstaat de zoutsproeicorrosie niet alleen aan het oppervlak, maar ook in het product.Het product wordt afwisselend omgezet tussen de zoutnevel en de vochtigheids- en hitteomgeving, en vervolgens moeten de elektrische en mechanische eigenschappen van het product op eventuele veranderingen worden beoordeeld.
Resultaatbepaling
Het testresultaat van de zoutsproeitest wordt doorgaans in kwalitatieve en niet in kwantitatieve vorm weergegeven.Er zijn vier specifieke bepalingsmethoden.
(1) Methode voor het bepalen van de beoordeling.
Bij deze methode verdeelt u de verhouding tussen het corrosieoppervlak en het totale oppervlak in verschillende niveaus en bepaalt u een bepaald niveau als gekwalificeerde basis voor de bepaling.Deze methode is geschikt voor de evaluatie van vlakke monsters.
(2) Methode voor het bepalen van het gewicht.
Door het gewicht van het monster voor en na de corrosietest te wegen, berekent u het gewicht dat verloren is gegaan door corrosie en beoordeelt u het gewichtbescherming tegen spuitcorrosiekwaliteit van het monster.Deze methode is bijzonder geschikt voor de beoordeling van de kwaliteit van de corrosieweerstand van bepaalde metalen.
(3) Methode voor statistische analyse van corrosiegegevens.
Deze methode biedt het betrouwbaarheidsniveau voor het ontwerpen van corrosietests, het analyseren van corrosiegegevens en het bepalen van corrosiegegevens, die voornamelijk worden gebruikt voor analyse en statistieken van corrosie, in plaats van specifiek voor het bepalen van de productkwaliteit.
Zoutsproeitest van roestvrij staal
Sinds de uitvinding in het begin van de twintigste eeuw is de zoutsproeitest zeer geliefd bij gebruikers van corrosiebestendige materialen vanwege de voordelen ervan, waaronder verminderde tijd en kosten, de mogelijkheid om een verscheidenheid aan materialen te testen en eenvoudige en duidelijke resultaten op te leveren.
In de praktijk is de zoutsproeitest van roestvrij staal het meest bekend en moeten praktijkmensen bekend zijn met hoeveel uur de zoutsproeitest voor dit materiaal kan duren.
Materiaaldealers verlengen vaak de zoutsproeitesttijd van roestvrij staal met methoden zoals passivering of het verhogen van de oppervlaktepolijstkwaliteit.De meest kritische bepalende factor is echter de samenstelling van het roestvast staal zelf, dat wil zeggen het gehalte aan chroom, molybdeen en nikkel.
Hoe hoger het gehalte aan zowel chroom als molybdeen, hoe groter de corrosieweerstand die nodig is om putcorrosie en spleetcorrosie te laten optreden.Deze corrosieweerstand wordt uitgedrukt in de zogenaamde putweerstandsequivalentwaarde (PRE): PRE = %Cr + 3,3 x %Mo.
Hoewel nikkel de weerstand van staal tegen putcorrosie en spleetcorrosie niet verhoogt, kan het wel effectief zijn bij het vertragen van de corrosiesnelheid zodra het corrosieproces is begonnen.Daarom hebben austenitische roestvaste staalsoorten die nikkel bevatten de neiging om veel beter te presteren in zoutsproeitests en veel minder te roesten dan ferritische roestvaste staalsoorten met een laag nikkelgehalte en vergelijkbare putweerstandsequivalenten.
Opgemerkt moet worden dat het zoutcorrosiebeschermingsspraytest heeft grote nadelen bij het testen van de prestaties van roestvrij staal.Het chloridegehalte van de zoutnevel in de zoutsproeitest is extreem hoog en overtreft ruimschoots de werkelijke omgeving. Roestvast staal dat corrosie kan weerstaan in daadwerkelijke toepassingen met een zeer laag chloridegehalte zal dus ook corroderen in de zoutsproeitest.
De zoutsproeitest verandert het corrosiegedrag van roestvrij staal, wat noch als een versnelde test, noch als een simulatie-experiment kan worden beschouwd.De resultaten zijn eenzijdig en hebben geen gelijkwaardige relatie met de daadwerkelijke prestaties van het uiteindelijk in gebruik genomen roestvast staal.
Je kunt dus de zoutsproeitest gebruiken om de corrosieweerstand van verschillende soorten roestvast staal te vergelijken, maar deze test kan alleen het materiaal beoordelen.Bij de keuze voor een specifiek RVS materiaal levert de zoutsproeitest alleen meestal niet voldoende informatie op, omdat het verband tussen de testomstandigheden en de daadwerkelijke toepassingsomgeving zelden bekend is.
Bovendien kunnen verschillende categorieën staal niet met elkaar worden vergeleken, omdat de twee in de test gebruikte materialen verschillende corrosiemechanismen hebben, waardoor de testresultaten en de relevantie van het uiteindelijke daadwerkelijke gebruik van het milieu niet hetzelfde zijn.
Posttijd: 08 juli 2022